Advantages of anti-corrosion for 4.8M diameter pipeline
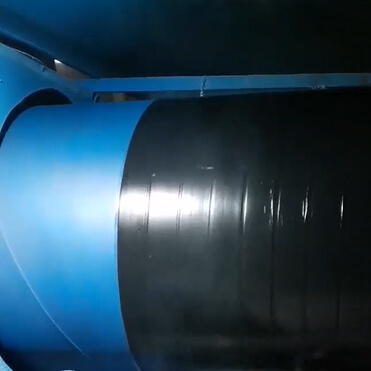
Improve pipeline safety: 1.1 Leak prevention: It can effectively resist various corrosive factors, reduce the probability of pipeline perforation, rupture and other leakage accidents caused by corrosion, ensure the safe and stable transportation of substances transported in pipelines (such as oil, natural gas, water, etc.), avoid environmental pollution, resource waste and potential safety hazards such as fires and explosions caused by leaks. For example, in oil transportation pipelines, anti-corrosion treatment can ensure that oil will not leak due to pipeline corrosion.
1.2 Maintaining structural integrity:
Anti corrosion measures help to maintain the strength and stiffness of pipelines, making them less prone to structural damage such as deformation and collapse when subjected to internal pressure, external loads, and soil or other media forces, ensuring that pipelines can stably perform their transportation functions during long-term use.
1.3 Extending the service life of pipelines:
By preventing or slowing down the corrosion process, the service life of pipelines can be significantly extended. Compared to pipelines that have not undergone anti-corrosion treatment, 4.8m large-diameter pipelines that have undergone good anti-corrosion treatment can continue to work for longer periods of time in harsh environments such as highly corrosive soil, seawater, etc., reducing the cost investment and project interruption caused by frequent pipeline replacement. Taking municipal water supply and drainage pipelines as an example, anti-corrosion treatment can increase the service life of pipelines by 1-2 times or even longer.
1.4 Reducing maintenance costs:
On the one hand, it reduces the frequent maintenance and replacement operations required due to corrosion damage, saving a lot of manpower, material resources, and financial resources. On the other hand, it reduces the frequency and intensity of maintenance during pipeline operation, making maintenance work easier and more efficient, and overall reducing the maintenance cost of the entire pipeline lifecycle.
2. Ensure conveying efficiency:
2.1 Reduce scaling and friction on the inner wall: Anti corrosion treatment can make the inner wall of the pipeline smoother, reduce the friction coefficient of the inner wall, reduce energy loss during fluid flow in the pipeline, and improve transportation efficiency. For example, in long-distance water pipelines, smooth inner walls can reduce water flow resistance and lower pump energy consumption.
2.2 Prevention of pipe diameter reduction:
Avoid rusting, scaling, or localized corrosion pits on the inner wall of the pipeline due to corrosion, thereby maintaining the effective inner diameter of the pipeline, ensuring stable conveying flow, and preventing the impact of pipe diameter reduction on conveying capacity.
2.3 Adaptation to complex environments:
Whether in humid underground environments, industrial environments containing corrosive chemicals, or harsh environments such as the ocean, anti-corrosion treatment can make large-diameter pipelines have good corrosion resistance, ensuring their reliable operation under different environmental conditions and expanding the application scope of pipelines. For example, in large drainage pipelines in coastal areas, anti-corrosion treatment enables them to resist the erosion of seawater and coastal air.
2.4 Compliance with environmental requirements:
Good anti-corrosion performance can reduce the pollution caused by pipeline corrosion to the surrounding environment, such as preventing harmful substances from leaking into soil or water, reducing damage to the ecological environment, and meeting the increasingly strict requirements of modern society for environmental protection.