An Overview of Furnaces Used in Steel Manufacturing
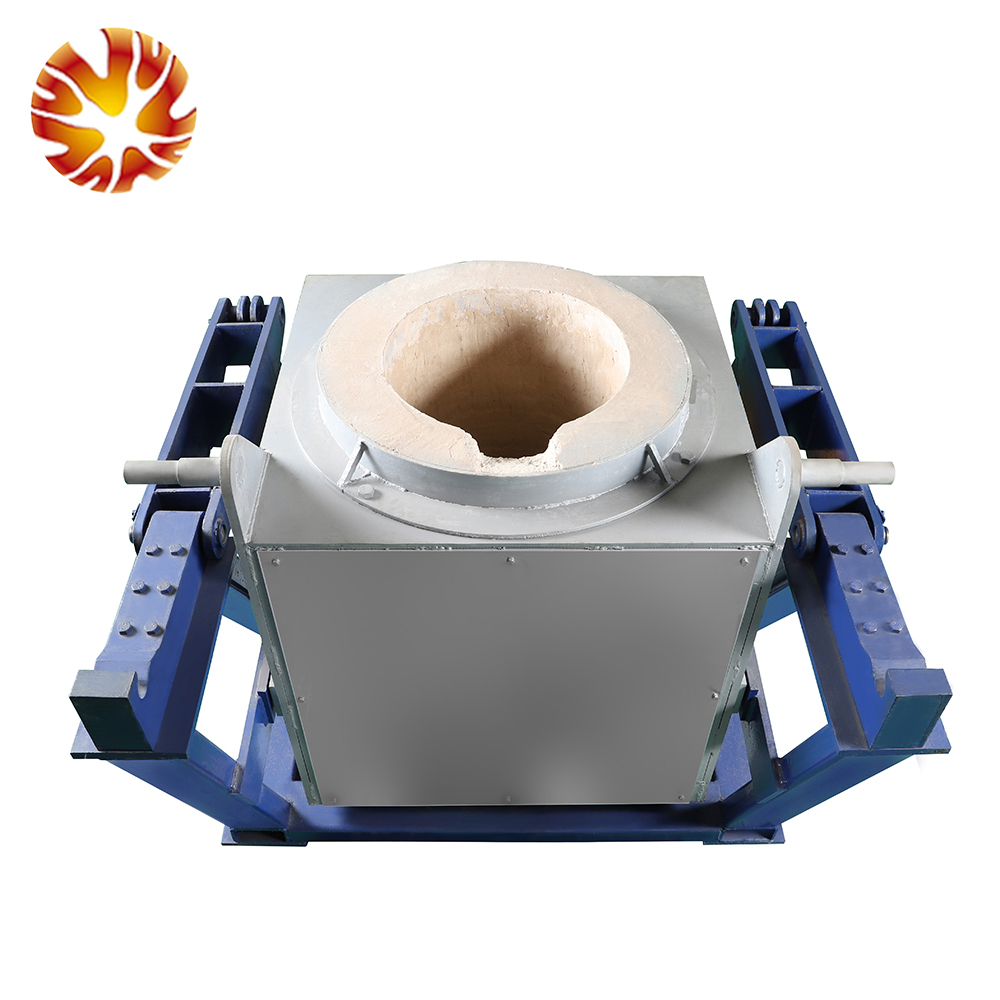
Furnaces play a crucial role in steel manufacturing. These devices enable the transformation of raw materials into high-quality steel. The history of furnace development in the steel industry dates back to the 19th century. Innovations such as the Bessemer process and open-hearth furnaces revolutionized modern steelmaking. The purpose of this blog is to explore different types of furnaces used in steel manufacturing, providing insights into their functionality and applications. What type of furnace is used for steel?
Blast Furnaces
Overview of Blast Furnaces
Historical significance
Blast furnaces have a rich history in the steel industry. The development of blast furnace technology dates back to the 14th century. Early versions were used in Europe for smelting iron ore. The Industrial Revolution brought significant advancements, making blast furnaces central to steel production.
Basic operation principles
A blast furnace operates by introducing a flow of air under pressure into the bottom of the furnace. This air reacts with a mixture of metallic ore, coke, and flux fed into the top. The reaction produces liquid metal and slag, which are then extracted from the bottom.
Features and Components
Structure and design
The structure of a blast furnace includes several key sections:
- Throat: The top part where raw materials are introduced.
- Stack: A vertical shaft where preheating occurs.
- Bosh: The widest section where temperatures reach their peak.
- Hearth: The bottom part where molten metal collects.
Key components
Key components of a blast furnace include:
- Tuyeres: Nozzles that inject air into the furnace.
- Refractory lining: Heat-resistant material that protects the structure.
- Charging system: Mechanism for adding raw materials.
- Tap hole: Outlet for extracting molten metal.
Pros and Cons
Advantages
Blast furnaces offer several advantages:
- High production capacity.
- Ability to produce high-quality steel.
- Efficient use of raw materials.
Disadvantages
However, there are also disadvantages:
- High energy consumption.
- Significant environmental impact due to emissions.
- Long start-up times.
Applications in Steel Manufacturing
Types of steel produced
Blast furnaces play a pivotal role in producing various types of steel. These furnaces primarily produce carbon steel, which forms the backbone of many industrial applications. Carbon steel offers high strength and durability, making it suitable for construction and automotive industries.
Blast furnaces also produce alloy steels by adding elements like chromium, nickel, and vanadium to the molten iron. Alloy steels exhibit enhanced properties such as increased hardness, corrosion resistance, and tensile strength. These characteristics make alloy steels ideal for specialized applications in aerospace and heavy machinery.
Specific use cases
The versatility of blast furnaces extends to numerous specific use cases:
- Construction Industry: Blast furnaces produce structural steel beams used in building skyscrapers, bridges, and other infrastructure projects. The high strength-to-weight ratio of carbon steel makes it an excellent choice for these applications.
- Automotive Sector: The production of automotive parts such as chassis, engine blocks, and body panels relies heavily on blast furnace output. Carbon steel’s durability ensures vehicle safety and longevity.
- Shipbuilding: Alloy steels produced in blast furnaces are essential for constructing ships and submarines. The corrosion-resistant properties of alloy steels ensure the longevity of vessels exposed to harsh marine environments.
- Pipeline Manufacturing: Blast furnaces contribute to the production of pipes used in oil and gas transportation. The robustness of carbon steel ensures that pipelines can withstand high pressure and extreme conditions.
- Railway Industry: Rails made from carbon steel produced in blast furnaces provide the necessary strength and wear resistance required for railway tracks.
“Blast furnace technology remains integral to modern industrial processes due to its ability to produce a wide range of high-quality steels,” according to studies on blast furnace advancements.
By understanding these applications, stakeholders can better appreciate the critical role that blast furnaces play in various sectors.
Electric Arc Furnaces (EAF)
Overview of Electric Arc Furnaces
Development and evolution
Electric Arc Furnaces (EAF) have transformed steel manufacturing. The development of EAF technology began in the late 19th century. Early versions were rudimentary but paved the way for modern advancements. By the mid-20th century, EAFs became more efficient and widely adopted.
Basic operation principles
EAFs operate by generating an electric arc between electrodes and the metal charge. This process melts scrap steel or direct reduced iron (DRI). Operators control the temperature precisely to achieve desired metallurgical properties. The furnace lining withstands high temperatures, ensuring durability.
Features and Components
Structure and design
The structure of an EAF includes several critical sections:
- Shell: A cylindrical container that holds the molten metal.
- Roof: A removable cover that contains electrodes.
- Electrodes: Graphite rods that create an electric arc.
- Furnace hearth: The bottom part where molten metal collects.
Key components
Key components of an EAF include:
- Transformer: Converts electrical energy to a suitable voltage.
- Water-cooled panels: Protects the furnace from excessive heat.
- Tapping system: Mechanism for extracting molten steel.
- Fume extraction system: Controls emissions during operation.
Pros and Cons
Advantages
Electric Arc Furnaces offer several advantages:
- Flexibility in raw material usage, including up to 100% scrap steel.
- Lower environmental impact due to reduced emissions.
- Faster start-up times compared to blast furnaces.
Disadvantages
However, there are also disadvantages:
- High electricity consumption can lead to increased operational costs.
- Dependency on stable electricity supply for consistent operation.
- Limited production capacity compared to traditional blast furnaces.
“The transition from blast furnaces to induction furnaces led to a 25% increase in production capacity,” according to industry case studies on furnace advancements.
By understanding these aspects, stakeholders can better appreciate how EAF technology contributes significantly to modern steel manufacturing processes.
Applications in Steel Manufacturing
Types of steel produced
Induction furnaces produce various types of steel. These include carbon steel, alloy steel, and stainless steel. Carbon steel offers high strength and durability. Alloy steel contains elements like chromium and nickel, enhancing properties such as hardness and corrosion resistance. Stainless steel resists rust and maintains a shiny appearance.
Specific use cases
Induction furnaces serve multiple industries with specific use cases:
- Construction Industry: Induction furnaces produce structural beams for buildings and bridges. The high strength-to-weight ratio of carbon steel ensures stability.
- Automotive Sector: Manufacturers rely on induction furnaces for engine blocks and body panels. The durability of carbon steel enhances vehicle safety.
- Aerospace Industry: Alloy steels from induction furnaces create aircraft components that withstand extreme conditions.
- Medical Equipment: Stainless steel from induction furnaces forms surgical instruments due to its corrosion resistance.
- Consumer Goods: Induction furnaces produce household appliances like refrigerators and washing machines using stainless steel for longevity.
“The transition from blast furnaces to induction furnaces led to a 25% increase in production capacity,” according to industry case studies on furnace advancements.
By understanding these applications, stakeholders can appreciate the critical role that induction furnaces play in various sectors.
Basic Oxygen Furnaces (BOF)
Overview of Basic Oxygen Furnaces
Historical context
Basic Oxygen Furnaces (BOF) emerged as a revolutionary technology in the mid-20th century. Engineers developed BOFs to address inefficiencies in earlier steelmaking methods. The introduction of BOFs marked a significant advancement over open-hearth furnaces. This innovation allowed for faster and more efficient steel production.
Basic operation principles
Basic Oxygen Furnaces operate by blowing oxygen through molten pig iron. This process reduces carbon content and other impurities. Operators introduce scrap metal to the furnace, which melts and mixes with the molten iron. The reaction generates intense heat, facilitating the conversion of raw materials into high-quality steel.
Features and Components
Structure and design
The structure of a BOF includes several critical sections:
- Converter vessel: A large, tiltable container that holds molten metal.
- Lance system: A device that injects high-purity oxygen into the converter.
- Refractory lining: Heat-resistant material that protects the vessel’s interior.
- Charging system: Mechanism for adding scrap metal and flux.
Key components
Key components of a BOF include:
- Oxygen lance: Delivers oxygen at high pressure to facilitate chemical reactions.
- Slag notch: Allows for the removal of slag formed during the process.
- Tap hole: Outlet for extracting molten steel from the converter.
- Gas cleaning system: Controls emissions produced during operation.
Pros and Cons
Advantages
Basic Oxygen Furnaces offer several advantages:
- High production efficiency due to rapid processing times.
- Ability to produce large quantities of steel in each batch.
- Enhanced control over metallurgical properties through precise oxygen injection.
Disadvantages
However, there are also disadvantages:
- Significant capital investment required for installation and maintenance.
- High energy consumption associated with oxygen production and delivery.
- Environmental impact due to emissions generated during operation.
“The shift to clean steel is not happening fast enough,” according to studies on electric arc furnace advancements.
Understanding these aspects helps stakeholders appreciate how Basic Oxygen Furnaces contribute significantly to modern steel manufacturing processes.
Applications in Steel Manufacturing
Types of steel produced
Electric Arc Furnaces (EAF) produce various types of steel. These include carbon steel, alloy steel, and stainless steel. Carbon steel offers high strength and durability. Alloy steels contain elements like chromium and nickel, enhancing properties such as hardness and corrosion resistance. Stainless steel resists rust and maintains a shiny appearance.
Specific use cases
Electric Arc Furnaces serve multiple industries with specific use cases:
- Construction Industry: EAFs produce structural beams for buildings and bridges. The high strength-to-weight ratio of carbon steel ensures stability.
- Automotive Sector: Manufacturers rely on EAFs for engine blocks and body panels. The durability of carbon steel enhances vehicle safety.
- Aerospace Industry: Alloy steels from EAFs create aircraft components that withstand extreme conditions.
- Medical Equipment: Stainless steel from EAFs forms surgical instruments due to its corrosion resistance.
- Consumer Goods: EAFs produce household appliances like refrigerators and washing machines using stainless steel for longevity.
“The transition from blast furnaces to electric arc furnaces led to a 25% increase in production capacity,” according to industry case studies on furnace advancements.
By understanding these applications, stakeholders can appreciate the critical role that Electric Arc Furnaces play in various sectors.
Induction Furnaces
Overview of Induction Furnaces
Development and evolution
Induction furnaces have revolutionized modern steel manufacturing. The development of induction furnace technology began in the early 20th century. Engineers sought efficient methods for melting metals without direct contact with fuel. Early models were rudimentary but laid the groundwork for significant advancements. By the mid-20th century, induction furnaces became more efficient and widely adopted in various industries.
Basic operation principles
Induction furnaces operate using electromagnetic induction to heat and melt metal. A coil generates a high-frequency alternating current (AC). This current creates a magnetic field that induces electric currents within the metal charge. These induced currents generate heat, causing the metal to melt. Operators control the temperature precisely, ensuring consistent metallurgical properties.
Features and Components
Structure and design
The structure of an induction furnace includes several critical sections:
- Crucible: A refractory-lined container that holds molten metal.
- Coil: An electromagnetic coil that generates the magnetic field.
- Cooling system: Mechanisms to prevent overheating of components.
- Power supply: Equipment that provides electrical energy to the coil.
Key components
Key components of an induction furnace include:
- Inductor: The primary component responsible for generating the magnetic field.
- Refractory lining: Heat-resistant material protecting the crucible’s interior.
- Tilting mechanism: Allows for easy pouring of molten metal.
- Control panel: Enables operators to adjust power levels and monitor temperatures.
Pros and Cons
Advantages
Induction furnaces offer several advantages:
- High energy efficiency due to direct heating of metal.
- Precise control over melting temperatures.
- Reduced environmental impact with lower emissions.
Disadvantages
However, there are also disadvantages:
- High initial capital investment for installation.
- Limited capacity compared to larger furnaces like blast furnaces.
- Dependency on stable electricity supply for consistent operation.
“The transition from traditional methods to induction furnaces led to a 25% increase in production capacity,” according to industry case studies on furnace advancements.
By understanding these aspects, stakeholders can better appreciate how induction furnace technology contributes significantly to modern steel manufacturing processes.
Applications in Steel Manufacturing
Types of steel produced
Induction furnaces produce various types of steel. These include carbon steel, alloy steel, and stainless steel. Carbon steel offers high strength and durability. Alloy steels contain elements like chromium and nickel, enhancing properties such as hardness and corrosion resistance. Stainless steel resists rust and maintains a shiny appearance.
Specific use cases
Induction furnaces serve multiple industries with specific use cases:
- Construction Industry: Induction furnaces produce structural beams for buildings and bridges. The high strength-to-weight ratio of carbon steel ensures stability.
- Automotive Sector: Manufacturers rely on induction furnaces for engine blocks and body panels. The durability of carbon steel enhances vehicle safety.
- Aerospace Industry: Alloy steels from induction furnaces create aircraft components that withstand extreme conditions.
- Medical Equipment: Stainless steel from induction furnaces forms surgical instruments due to its corrosion resistance.
- Consumer Goods: Induction furnaces produce household appliances like refrigerators and washing machines using stainless steel for longevity.
“The transition from blast furnaces to induction furnaces led to a 25% increase in production capacity,” according to industry case studies on furnace advancements.
By understanding these applications, stakeholders can appreciate the critical role that induction furnaces play in various sectors.
The blog discussed the various types of furnaces used in steel manufacturing. These include blast furnaces, electric arc furnaces, basic oxygen furnaces, and induction furnaces. Each furnace type offers unique advantages and disadvantages.
Choosing the right furnace for specific steel manufacturing needs is crucial. The selection impacts production efficiency, cost-effectiveness, and environmental sustainability.
Future trends in furnace technology focus on improving energy efficiency and reducing emissions. Innovations aim to enhance operational flexibility and metallurgical control.
Furnaces play an essential role in the steel industry. They enable the transformation of raw materials into high-quality steel products that drive industrial progress.