Best Furnaces for Efficient Metal Heating
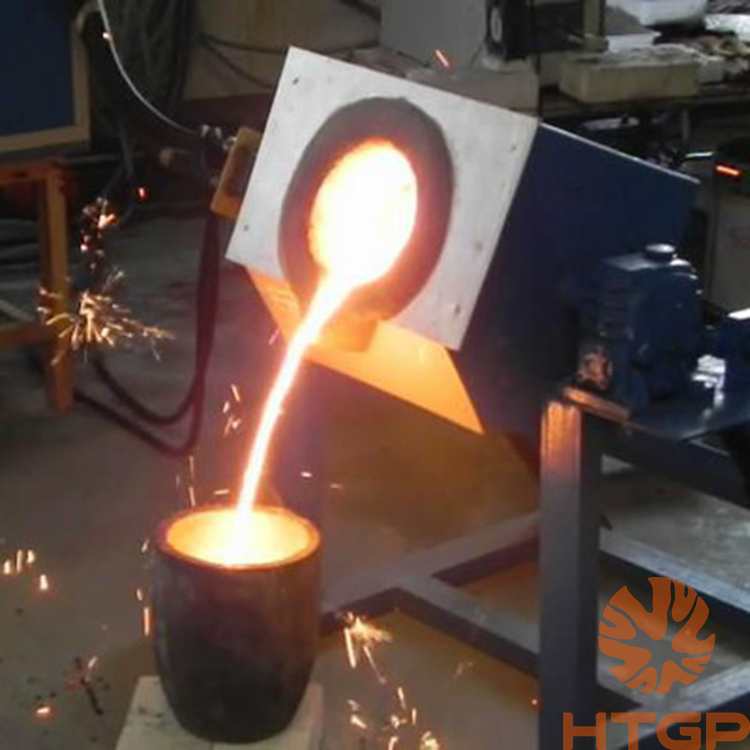
Efficient metal heating is paramount in industrial processes, impacting energy consumption and production quality. Various types of furnaces, such as Furnace, play a crucial role in achieving optimal temperatures for smelting and casting metals. This blog aims to provide a comprehensive guide for selecting the most suitable furnace based on specific needs and applications.
Types of Furnaces
Induction Furnaces
Induction furnaces operate on the principle of electromagnetic induction. They utilize this phenomenon to generate heat within the metal by inducing electrical currents. This process enables efficient melting of various non-ferrous metals like copper and aluminum. The utilization of electromagnetic fields distinguishes induction furnaces from other types, making them ideal for precise metal heating applications.
Working Principle
- Electromagnetic induction for heat generation
- Efficient melting of non-ferrous metals
Advantages
- Rapid heating process
- Energy-efficient operation
- Precise temperature control
Disadvantages
- Initial high setup costs
- Limited to non-ferrous metal melting
Electric Arc Furnaces
Electric arc furnaces rely on the creation of an electric arc between two electrodes to produce intense heat required for metal melting processes. These furnaces are commonly used in iron and steel production, as well as for melting scrap materials, contributing significantly to sustainable metal manufacturing practices.
Working Principle
- Creation of electric arc for heat generation
- Melting steel and other metals efficiently
Advantages
- Flexibility in raw material usage
- High-quality end products
- Reduced environmental impact
Disadvantages
- Dependence on electricity supply
- Maintenance of electrodes required
Blast Furnaces
Blast furnaces are traditional metallurgical furnaces that use combustion reactions fueled by coke or coal to smelt industrial metals such as pig iron and lead. These furnaces have been fundamental in large-scale metal production processes due to their ability to handle high capacities and continuous operations.
Working Principle
- Combustion reactions with coke or coal for smelting
- Suitable for large-scale metal production
Advantages
- High-capacity operations
- Continuous smelting process
- Cost-effective production
Disadvantages
- Environmental concerns
- Limited flexibility in product variations
Crucible Furnaces
Working Principle
Crucible furnaces operate by using a refractory crucible to contain the metal during the heating process. The furnace applies heat externally to melt metals with relatively low melting points like brass, bronze, and aluminum. This method ensures precise temperature control and efficient melting for various casting applications.
Advantages
- Facilitates melting of low-melting-point metals
- Enables controlled heating processes
- Ideal for small-scale casting operations
Disadvantages
- Limited capacity for large-scale production
- Requires frequent maintenance due to high operating temperatures