Heating treatment and electromagnetic conversion of induction furnace
How does an intermediate frequency induction furnace convert electrical energy into heat energy to heat metal during heating?
Theoretically speaking, the intermediate frequency induction furnace heating process consists of two stages.
The first stage: the alternating current of the frequency conversion device of the medium frequency induction furnace generates alternating magnetic field
When the alternating frequency current of the medium frequency induction furnace passes through the spiral induction coil, a magnetic field is generated in and around the space enclosed by the coil.
The polarity and strength of the magnetic field vary with the frequency of the alternating current. Part of the magnetic line of force penetrates the metal charge, and part penetrates the lining material.
The polarity, intensity and rate of flux change of the magnetic field, that is, the direction of the magnetic field and the number and density of magnetic field lines, are determined by the intensity of the current passing through the induction coil, the frequency, the number of turns and the geometric size of the coil.
The second stage: the alternating magnetic field of the frequency conversion device of the intermediate frequency induction furnace generates induced current
A part of the magnetic field line penetrates the metal charge, which is equivalent to the conductor for cutting the magnetic line of force, so that the induced electromotive force E is generated in the closed loop formed between the metal charge.
The relative size of the main flux and the leakage flux can be affected by many factors,
The thicker the crucible and the smaller the furnace, the more leakage flux and the less main flux. Therefore, the newly knotted crucible has more leakage flux. After melting a few furnaces, the crucible becomes thinner and the leakage flux is reduced.
The distribution of magnetic field will be affected by the different metal materials in smelting.
When smelting copper and aluminum and other metals, due to low resistivity and greater penetration than steel, the eddy current loop induced in copper and aluminum has smaller resistance, so when the medium frequency main flux enters the copper and aluminum, it is offset by the induction eddy current, resulting in the reduction of the main flux.
Remember that the temperature of the hot metal should be accurately controlled, and that the temperature of the electric furnace should not be too high or locally too high. This is not conducive to power consumption and lining life. A good feeder saves power and improves efficiency.
The same large electric furnace can save electricity quickly, the same fast electric furnace can save electricity greatly, and the high voltage saves electricity more than the low voltage. Casting time also affects power consumption, preferably within 5-10 minutes.
That’s it for today. I hope you found it helpful. Welcome to Luoyang Hongteng for more information about induction furnace.
Video of the use process of the furnace
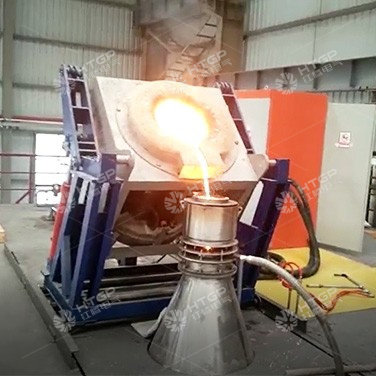