High-Performance Smelting Furnaces Compared
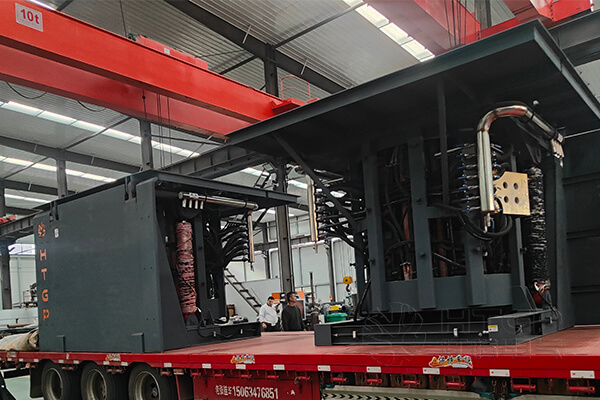
In the realm of industrial operations, smelting furnaces stand as the backbone of metal production, embodying efficiency and precision. High-performance smelting furnaces, a pinnacle of innovation, redefine the standards of productivity and quality in metalworking. This blog embarks on a journey to dissect and compare various high-performance furnaces, shedding light on their unique features and benefits. By delving into this furnace fiesta, readers can uncover the best furnace tailored to their needs.
Overview of High-Performance Smelting Furnaces
Definition and Importance
High-Performance Smelting Furnaces:
Metal melting furnaces, like those manufactured by Charles A. Hones, Inc., redefine efficiency in industrial operations. These furnaces come in various sizes, from 160 lbs. lead capacity to a substantial 2,700 lbs., catering to diverse melting needs with precision and reliability.
Key Benefits and Applications
- Versatile Melting Capabilities: The wide temperature range of MIFCO High Speed Melters enables the melting of most non-ferrous metals used in casting, ensuring flexibility in metalworking processes.
- Rapid Melting Efficiency: Designed to reach temperatures between 1200°F to 2400°F swiftly, these furnaces prioritize speed without compromising quality.
- Alloy Compatibility: High-performance smelting furnaces excel in melting lead, tin, solder, babbitt, bismuth, pewter, and related soft metals and their alloys with ease.
Technological Advancements
Innovations in Furnace Design
- Advanced Heating Mechanisms: The incorporation of cutting-edge heating technologies enhances the efficiency and speed of the melting process.
- Precision Control Systems: Modern high-performance furnaces boast intricate control systems that ensure accurate temperature regulation for optimal metal melting results.
Impact on Efficiency and Output
- Enhanced Productivity: The rapid heating capabilities of these furnaces significantly reduce downtime during the smelting process.
- Improved Quality Standards: By maintaining precise temperatures throughout the melting phase, high-performance furnaces guarantee consistent quality output for various industrial applications.
Key Features of High-Performance Smelting Furnaces
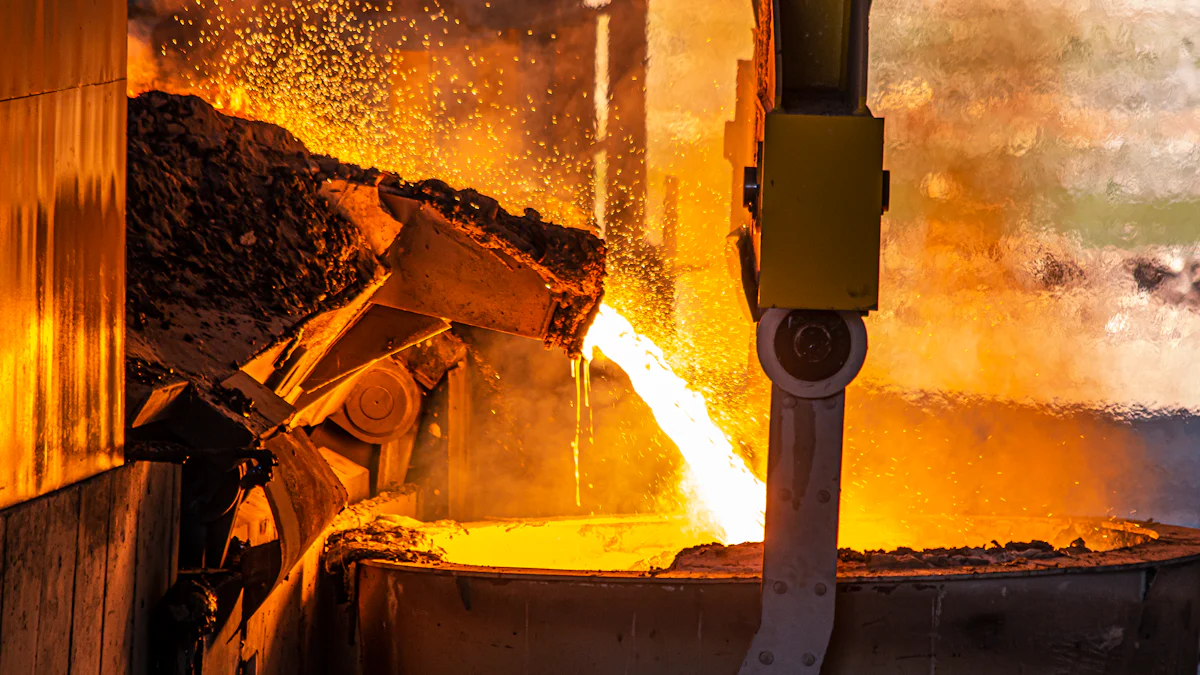
Energy Efficiency
Energy Consumption Metrics
- Comparing the efficiency of 80% and 95% furnaces reveals substantial differences in energy consumption.
- Metal melting furnaces exhibit varying energy usage levels, impacting operational costs and environmental sustainability.
- Understanding these metrics is crucial for optimizing resource utilization and minimizing energy expenses.
Cost Savings and Environmental Impact
- High-performance smelting furnaces offer significant cost savings through enhanced energy efficiency.
- Investing in a furnace with superior energy performance not only reduces operational expenses but also contributes to a greener environment.
- The choice between different furnaces can directly influence financial savings and ecological footprint.
Temperature Control
Precision and Stability
- Precision temperature control is a hallmark feature of advanced smelting furnaces, ensuring accurate melting processes.
- Maintaining stable temperatures throughout the smelting operation guarantees consistent material quality and output reliability.
- The ability to regulate heat with precision enhances overall productivity and product integrity.
Impact on Material Quality
- Effective temperature control directly impacts the quality of melted metals, influencing their structural properties.
- High-performance furnaces facilitate the production of materials with superior purity, strength, and consistency.
- Optimal temperature management results in high-quality end products suitable for diverse industrial applications.
Durability and Maintenance
Material and Build Quality
- Evaluating the durability of smelting furnaces involves assessing the materials used in construction and overall build quality.
- Robust construction materials enhance longevity and reliability, ensuring prolonged operational efficiency.
- Investing in a furnace with superior material quality safeguards against premature wear and maintenance issues.
Maintenance Requirements and Longevity
- Understanding the maintenance demands of high-performance furnaces is essential for long-term operational success.
- Regular upkeep routines prolong furnace lifespan, reducing downtime and repair costs over time.
- Prioritizing maintenance tasks ensures consistent performance and extends the longevity of smelting equipment.
Comparison of Leading High-Performance Smelting Furnaces
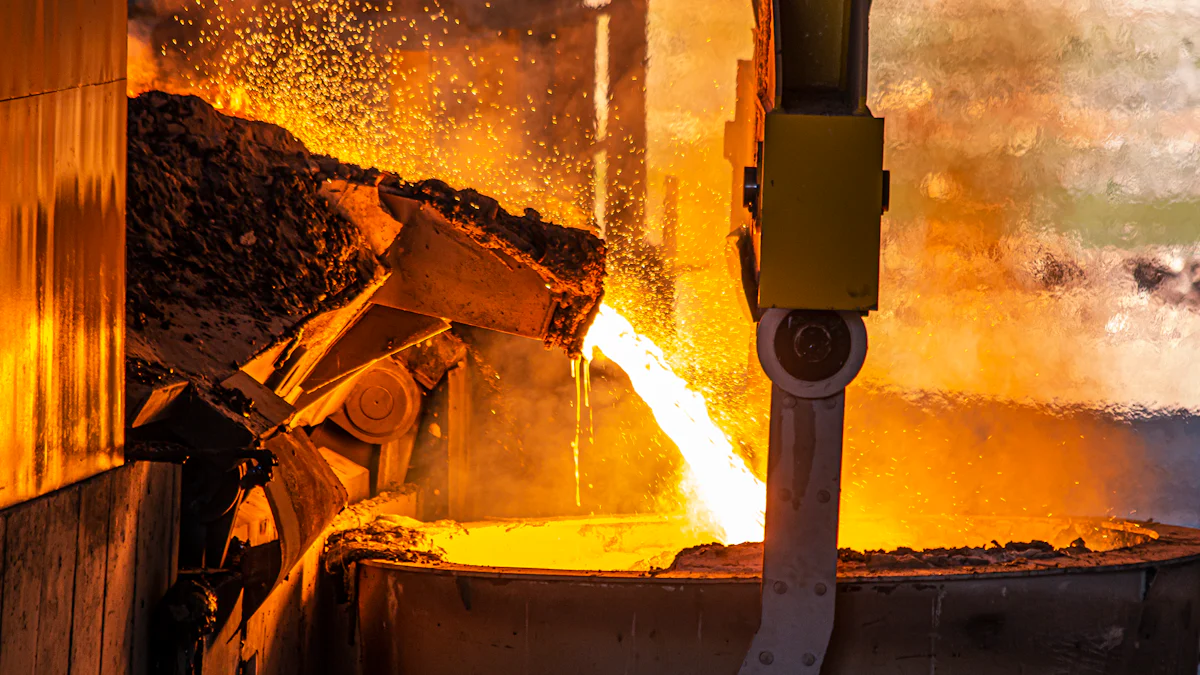
Propane Furnaces
Key Features
- Versatility: Capable of melting various metals efficiently.
- Affordability: Budget-friendly option for beginners.
- Convenience: Easy to use and suitable for backyard settings.
Pros and Cons
Pros:
- Provides a cost-effective solution for small-scale operations.
- Offers portability and flexibility in metalworking projects.
Cons:
- Limited capacity compared to larger furnaces.
- May require more frequent refills during extended use.
Induction Furnaces
Key Features
- Efficiency: Generates heat directly within the material for rapid melting.
- Precision: Ensures accurate temperature control and consistent results.
- Adaptability: Suitable for a wide range of metals, including copper and aluminum.
Pros and Cons
Pros:
- High energy efficiency leading to cost savings over time.
- Ideal for applications requiring precise temperature management.
Cons:
- Initial investment cost may be higher than other furnace types.
- Requires specialized knowledge for optimal operation.
Electric Arc Furnaces (EAF)
Key Features
- High-Temperature Melting: Suited for melting metals at extreme temperatures.
- Durability: Constructed to withstand intense heat and heavy usage.
- Versatility: Capable of handling a variety of metal types and alloys.
Pros and Cons
Pros:
- Efficient in melting high-melting-point metals like steel or iron.
- Offers flexibility in production processes due to its versatility.
Cons:
- Energy-intensive operation leading to higher electricity costs.
- Maintenance requirements can be complex, requiring skilled technicians.
Blast Furnaces
Key Features
- Robust Construction: Blast furnaces are known for their sturdy build, capable of withstanding high temperatures and heavy usage.
- High Melting Capacity: These furnaces offer substantial melting capacities, making them ideal for large-scale industrial applications.
- Versatile Applications: Blast furnaces can efficiently melt a wide range of metals, from iron to copper, catering to diverse smelting needs.
Pros and Cons
Pros:
- Efficient Melting Process: Blast furnaces ensure quick and thorough melting of metals, enhancing operational efficiency.
- Industrial Scale Production: Ideal for industries requiring mass metal production due to their high capacity and reliability.
Cons:
- Energy Intensive Operation: The operation of blast furnaces can lead to higher energy consumption levels.
- Maintenance Demands: Regular maintenance is crucial for optimal performance, which may require skilled technicians.
Notable Brands and Models
ToAuto TGF3000 Melting Furnace
- The ToAuto TGF3000 Melting Furnace stands out as a top-tier choice for those seeking the best furnace in terms of performance and durability. With its advanced features and robust design, it ensures efficient metal melting processes.
QuikMelt Pro 10 oz Melting Furnace
- The QuikMelt Pro 10 oz Melting Furnace is a compact yet powerful furnace designed for artists and small-scale metalworkers. Its user-friendly interface and reliable performance make it a popular option in the market.
VEVOR Stainless Steel 6KG Smelting Furnace Kit
- The VEVOR Stainless Steel 6KG Smelting Furnace Kit offers a balance between capacity and efficiency. Its durable construction and precise temperature control make it a reliable choice for various smelting applications.
Handy Melt 110 v., 30 T. oz. capacity furnace
- The Handy Melt 110 v., 30 T. oz. capacity furnace is renowned for its versatility and ease of use. Whether you’re working on intricate projects or larger productions, this furnace provides consistent results with minimal effort.
Gas Metal Melting Furnace FB3H – 20Kg Full Kit by DEVIL-FORGE
- The Gas Metal Melting Furnace FB3H by DEVIL-FORGE is a powerhouse in the smelting world, offering a generous melting capacity of up to 20kg. Its comprehensive kit includes everything you need for efficient metal melting processes.
Recommendations and Considerations
Choosing the Right Furnace
Factors to Consider
- Evaluate your metalworking needs and production scale before selecting a furnace.
- Consider the types of metals you frequently work with to ensure compatibility with the furnace.
- Assess the available space for installation and operation to determine the appropriate furnace size.
- Research the energy efficiency ratings of different furnaces to optimize operational costs.
- Examine the temperature control features to guarantee precise melting processes.
Industry-Specific Needs
- Analyze industry standards and regulations to align furnace specifications with compliance requirements.
- Consult with experienced professionals in your field to gain insights into specialized furnace functionalities.
- Explore case studies or success stories from similar industries to understand ideal furnace choices.
- Attend trade shows or exhibitions showcasing industrial furnaces for hands-on comparison and evaluation.
- Seek recommendations from reputable suppliers or manufacturers known for quality and reliability.
Cost vs. Performance
Budget Considerations
- Establish a clear budget range based on your financial capacity and long-term investment goals.
- Compare initial purchase costs, operational expenses, and maintenance fees across different furnace models.
- Factor in potential energy savings and productivity gains when evaluating overall cost-effectiveness.
- Look for financing options or payment plans that align with your budget constraints without compromising quality.
- Prioritize value over price by considering durability, efficiency, and performance as key determinants of long-term cost benefits.
Long-Term Value
- Focus on the total cost of ownership rather than upfront expenses to assess the true value of a high-performance furnace.
- Project future growth and expansion needs to ensure scalability and adaptability of the chosen furnace model.
- Invest in preventive maintenance programs or extended warranties to safeguard against unexpected repair costs.
- Monitor industry trends and technological advancements to stay ahead of evolving smelting requirements for sustained value.
- Seek feedback from existing users or experts in the field to validate claims of durability, reliability, and performance longevity.
By carefully weighing these considerations, you can confidently select a high-performance smelting furnace that not only meets your current needs but also anticipates future demands with efficiency and excellence in metalworking operations!
- In summary, the blog explored the diverse features and benefits of high-performance smelting furnaces, highlighting their efficiency and technological advancements.
- The best high-performance smelting furnace ultimately depends on individual needs and preferences, with options ranging from propane to induction furnaces.
- Readers are encouraged to share their experiences and insights on choosing the ideal furnace for their metalworking endeavors.
-
Take action now by subscribing for more insightful reviews and updates on high-performance smelting furnaces!