How do you melt steel? Method of induction heating in electric furnace
Steel is a valuable and useful resource in the manufacture of cars, planes and trains. We really can’t get around without it. However, the tools we use to melt and shape this metal are just as important. Without an induction furnace, the process of melting metal would be difficult.
When we use steel, induction heating is an ideal heating method, can be controlled by heating depth and heating time, to meet the surface quenching requirements of the workpiece.
Induction heating can be used in the following scenarios:
Diathermy: During the heating process, the internal and surface temperatures of the whole workpiece are roughly equal, which is called diathermy. Induction heating for dithermic heating has the advantages of high heating efficiency, fast speed, reduce metal burning loss, easy to control the temperature, to ensure the quality of heating, so it has been more and more widely used.
Smelting: When induction furnace is used for smelting, it has these advantages, can provide workers with a better working environment, high heating efficiency, less burning loss of alloying elements in the solution, easy control of the composition, high quality products, especially suitable for melting various high-grade alloy steel.
Sintering: Sintering is used in powder metallurgy, commonly used to make carbide cutting tools and other products. Induction heating is an ideal heating method for vacuum sintering, which can improve the quality of products.
The melting point of steel is as high as 1370℃. It takes more than a simple furnace to melt and shape this strong metal.
Induction furnace is mainly composed of intermediate frequency power supply and melting furnace body, supporting equipment including transformer, closed cooling tower and so on.
There are many types of induction furnace, which can be designed according to the needs of users. For example, specifically for smelting steel or specifically for smelting aluminum.
Its capacity is also designed to be flexible, depending on the size of the furnace, which can reach 0.5-15T per hour.
Furnace heating process through induction coil to achieve, every less than 1 hour can complete the metal smelting, the speed is very fast, and the work is very stable.
Induction furnace can work continuously for 24 hours. When in use, no noise during operation, in line with environmental standards.
After the metal is melted, the molten steel needs to be poured out, which can be turned over using a reducer or a hydraulic tilt to make the pouring process safer.
Some excellent induction furnace manufacturers will also design leakage furnace alarm device and melting management system for electric furnaces, so that the use of induction furnace process is more convenient and safe.
With a molten steel induction furnace, each design is configured down to the last detail before the steel is melted. Then, you can start the melting process. Because steel has such a high melting point, a unique furnace is needed to melt it to a usable temperature.
A furnace can change this hard metal into hot iron. The final product is then packaged and shipped to the manufacturer. Induction melting furnaces are more efficient than conventional gas furnaces. Not only do they distribute heat more evenly, but they also improve the environment significantly by releasing less waste and gases into the air.
Welcome to pay attention to our Luoyang Hongteng, you can learn more about induction furnace and metal melting knowledge.
Video of the use process of the furnace
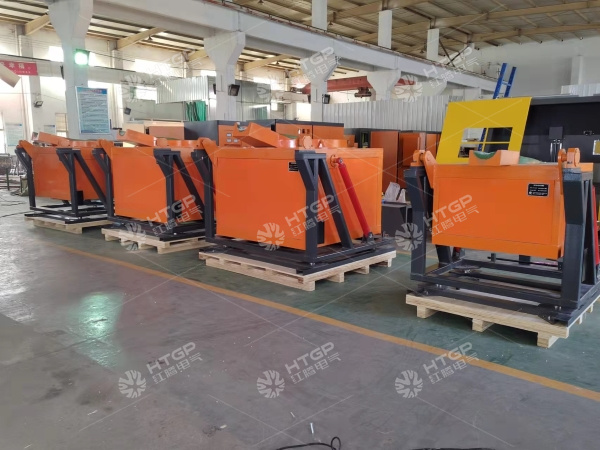