How should the lining of the electric furnace be knotted?
When the electric furnace is working, not only the temperature in the furnace is high and the change is large, but also it is subjected to strong electromagnetic stirring and the impact of the charging charge, which will cause the lining of the electric furnace to be easily damaged.
Therefore, the quality of the lining of the induction furnace directly determines the life of the furnace, which will ultimately affect the production capacity of the entire production line.
We previously had an article “Construction Method of Knotted Material for Intermediate Frequency Furnace”, which once introduced the knowledge of knotting of furnace lining to you. Today, let’s expand it and share some knowledge about furnace lining sintering.
After the furnace lining is finished, the furnace and sintering process can be carried out. The purpose is to fully remove the moisture in the furnace lining, so that the silica sand is fully and uniformly transformed, and finally sintered at high temperature into a dense ceramic surface with high strength.
When baking and sintering, we need to pay attention to the following items:
Before the oven, a detailed inspection of the water cooling system, tilting system, control loop and various markings should be carried out.
A certain amount of charge must be added during the oven, which is about 70% of the height of the furnace to ensure the uniformity of temperature rise and fall.
The oven should adopt low power, slow heating, and cooling water should be passed through while power is being supplied. In the initial stage of the oven, the heating rate is 100°C/h and the temperature rises evenly until 800-900°C.
Use clean and rust-free return materials to reduce slag, among which large pieces should be installed around the crucible wall, and small pieces should be added at the center of the furnace bottom.
The temperature of the molten iron should be about 50°C higher than the working temperature, and it should be maintained for 1-2 hours to make the furnace lining evenly sintered. The entire melting time of the first furnace is about 2-3 times the normal melting time.
After the first furnace is melted, the sintered layer of the crucible is still very thin, and the sintering process can only be completed after continuous melting for 2-3 furnaces.
If the sintering temperature is too low and the holding time is not enough, the lining will crack after cooling.
This is our knowledge sharing today, about the furnace process of electric furnace lining. Hope it helps you.
Welcome to Luoyang Hongteng, let us provide you with more services.
Video of the use process of the furnace
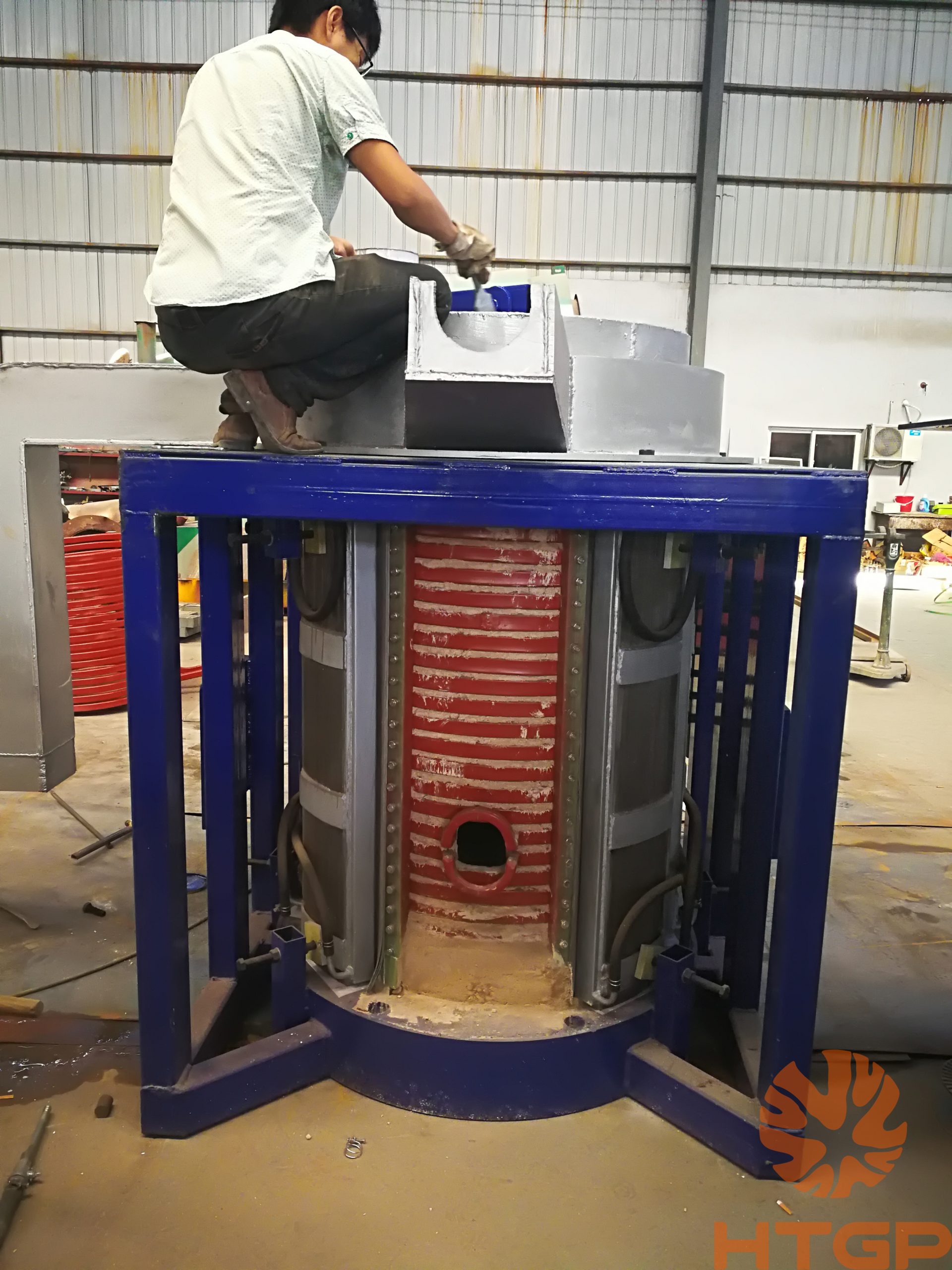