How to make induction furnace more power-saving when working
Induction furnaces are mainly used to smelt metals, and in the process of use, the consumption of electricity is very large. Therefore, for many users, how to reduce the power consumption of induction furnaces is a very important thing to solve. Today we will introduce some methods to you.
1. On the premise of ensuring the normal operation of workers, the production site should try to maintain a smaller space layout, which can shorten the connection lines of the production line, reduce the loss caused by current transmission, and save electricity.
2. When designing the furnace body, it is necessary to select the appropriate furnace body size and induction coil to ensure the smooth flow of current and improve the heating efficiency of the induction coil.
3. Control the temperature of molten steel. This requires the operators of the production line to pay attention to the working conditions of the induction furnace at any time, identify the timing of feeding, to assist in stirring the steel, and improve the melting speed of the metal. Doing this can reduce power consumption very well.
4. Each manufacturer has its own production process and equipment materials. If some manufacturers use inferior and thinner copper materials, the power consumption of the electric furnace will become higher and higher. Therefore, we need to choose the right equipment manufacturer.
5. When preheating the furnace body, turn off the cooling water of the induction coil, keep one-third of the normal water volume, and keep the outlet water temperature above 55 degrees to facilitate the smooth discharge of water vapor. This work can shorten the preheating time of the furnace body, and also help us save electricity.
The above is the knowledge shared by Luoyang Hongteng editors about reducing the power consumption of induction furnaces.
Welcome to follow us, let us solve more doubts about induction furnace for you.
Video of the use process of the induction furnace
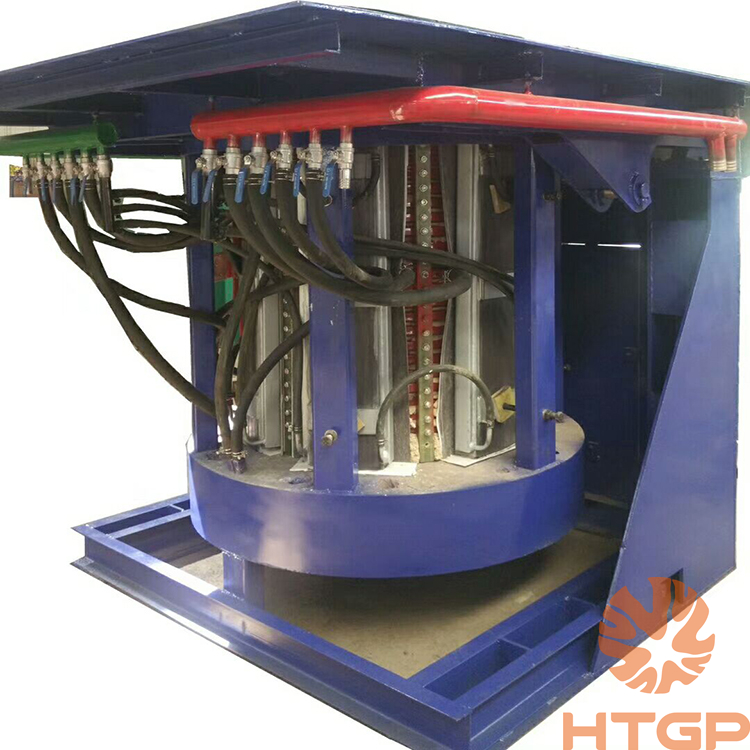