What Is Slab Continuous Casting?
Slab continuous casting is a casting method used in the steelmaking industry to produce flat, rectangular slabs of steel. Today, we will introduce the details to you.
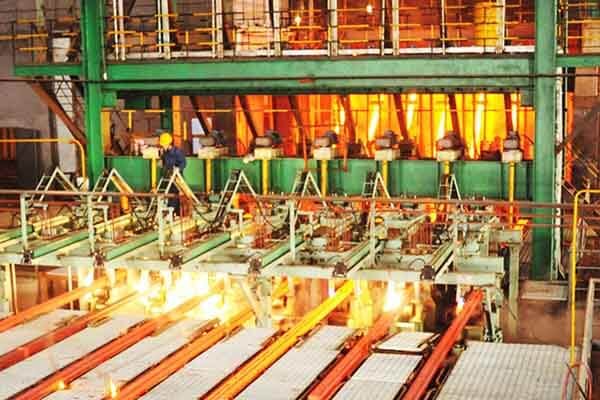
Slab Continuous Casting Process
The process involves the continuous casting of molten steel into a water-cooled copper mold, which solidifies and forms the shape of the slab.
Here are the basic steps involved in slab continuous casting:
Preparation of the Mold
The copper mold is prepared by cooling it with water to form a solid shell. The mold is then coated with a lubricant to prevent the steel from sticking to it.
Charging the Furnace
A furnace is charged with scrap steel and other materials and heated to a temperature of around 1,600-1,800°C (2,912-3,272°F), melting the steel.
Tapping the Furnace
The molten steel is then tapped from the furnace and poured into a ladle.
Refining the Steel
The steel is then refined in the ladle to remove impurities and adjust its chemical composition.
Pouring the Steel
The ladle is then tilted and the molten steel is poured into the copper mold. As the steel enters the mold, it begins to cool and solidify.
Moving the Slab
As the steel continues to solidify, it is gradually pulled through the mold by a series of rollers, while water is sprayed on the mold to cool it and solidify the steel.
Cutting the Slab
Once the slab has fully solidified, it is cut into the desired length using a torch or saw.
Finishing the Slab
The slab may undergo further processing, such as rolling or heat treatment, to achieve the desired properties and dimensions.
Advantages of Slab Continuous Casting
Slab continuous casting offers several advantages over traditional ingot casting methods, including:
Higher Productivity
The continuous casting process allows for a steady and uninterrupted flow of steel, which increases productivity compared to batch processes.
Improved Quality Control
The continuous casting process ensures consistent quality and fewer defects than traditional ingot casting methods. The controlled cooling process also allows for precise control of the microstructure of the steel.
Reduced Energy Consumption
Continuous casting is more energy-efficient than traditional ingot casting methods because it requires less energy to heat and melt the steel.
Reduced Material Waste
The continuous casting process produces less material waste compared to traditional ingot casting because it can be used to produce slabs of the exact size and shape required, minimizing the need for further cutting and processing.
Lower Production Costs
The higher productivity improved quality control, and reduced material waste associated with continuous casting can result in lower production costs compared to traditional ingot casting methods.
Slab continuous casting is a highly efficient and cost-effective process that has become the preferred method for producing slabs and other flat steel products in the steel industry.