What type of furnace is used for steel?
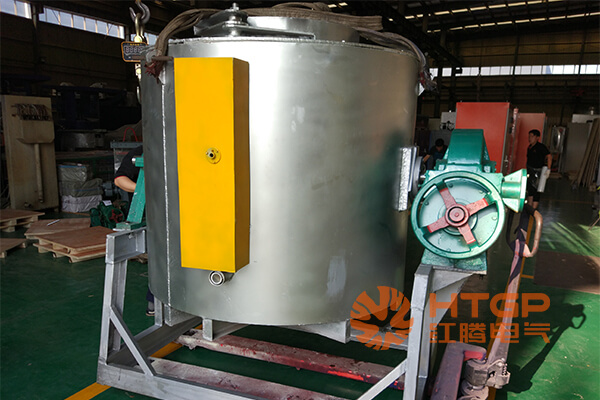
Steel production is an extremely important industrial process, the transformation of which relies heavily on the choice of steel furnaces. The furnaces play a key role in determining the quality and efficiency of steelmaking. Throughout history, various types of steel furnaces have been used, each making a unique contribution to the evolution of steel production methods. Understanding the importance of these furnaces is essential to grasping the complexity of the steelmaking process.
Types of furnaces used in steelmaking
The blast furnace is the cornerstone of steel production and has a long history of continuous evolution.
The blast furnace operates by burning coke and limestone to produce high heat to smelt iron ore. Over time, blast furnace methods have been continuously improved to increase efficiency and output.
Historically, the blast furnace revolutionized the steelmaking process by enabling large-scale production.
Innovations in blast furnace design have increased productivity and reduced energy consumption. The evolution of the blast furnace reflects the steel industry’s commitment to progress and sustainability.
The working principle of the blast furnace is simple and effective: iron ore is reduced to molten iron through high-temperature combustion.
The process relies on precise control of airflow and raw material ratios to achieve optimal results.
Advantages and DisadvantagesAdvantages:High production capacityWell-established and widely adopted infrastructureEfficient use of raw materialsDisadvantages:Large greenhouse gas emissionsDependence on non-renewable resources such as cokeLimited flexibility in product customization
The steel industry is committed to sustainable development, aiming to reduce carbon emissions and promote environmentally friendly practices. Steel manufacturers are developing greener technologies that prioritize energy efficiency and emissions control.