Continuous casting
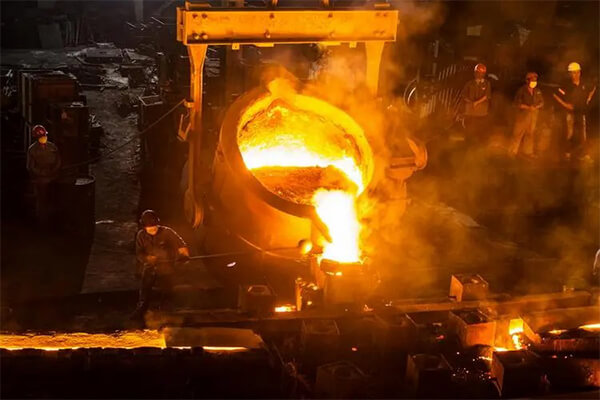
- Melting:
Raw materials are melted in a furnace to form molten metal. Molten metal is often purified to remove impurities.
- Casting:
Molten metal is poured into water-cooled molds, usually made of copper, to obtain the desired shape and size of the final product. The mold is often shaken or rotated to promote even cooling and solidification.
- Solidification:
As the molten metal flows through the mold, it begins to solidify along the mold walls due to the water wall. The solidification process continues until the metal emerges from the bottom of the mold into a solidified blank, slab, or other shape, depending on the requirements.
- Continuous operation:
Unlike traditional casting methods, continuous casting allows a continuous flow of metal, enabling mass production and consistent quality.
Continuous casting offers several advantages over traditional methods, including increased productivity, improved product quality, and reduced energy consumption and production costs.
It is widely used in the steel and aluminum industries to produce a variety of products such as billets, slabs, blooms and rods, which are then further processed into finished products such as automotive parts, construction materials and consumer products.