What Are the Advantages of Induction Melting Furnace in Metallurgy?
There are many types of melting furnaces in metallurgy, such as the electric arc furnace (EAF), the induction melting furnace, the gas/oil-fired furnace, and the resistance furnace. Every type of melting furnace has its own features. Now let’s see together.
Melting Furnaces Types and Their Features
Electric Arc Furnace (EAF)
An EAF uses electric arcs between electrodes to melt metals. This type of furnace is commonly used for recycling scrap metal, as it can quickly heat and melt large amounts of metal.
Induction Melting Furnace
An induction furnace uses electromagnetic induction to heat and melt metal. The most common furnaces are induction aluminum melting furnaces, induction copper melting furnaces, and induction stainless steel melting furnaces.
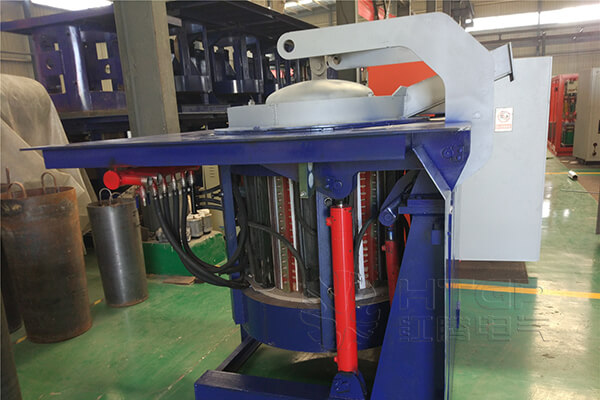
Gas/Oil Fired Furnace
A gas/oil-fired furnace uses natural gas or propane as a fuel source to heat and melt metal. This type of furnace is commonly used for melting non-ferrous metals like copper and aluminum.
Resistance Furnace
A resistance furnace uses resistance heating elements to generate heat and melt metal. This type of furnace is commonly used for small-scale heating and melting applications.
The specific type of melting furnace used depends on the type of metal being melted, the required production output, and the specific application requirements.
However, as time goes by, the induction melting furnace becomes more and more popular because it has many advantages compared to regular furnaces.
Several Advantages of Induction Melting Furnaces in Metallurgy
High Efficiency: Induction melting furnaces are highly efficient in converting electrical energy into heat due to the electromagnetic field generated by the induction coil. This results in quicker melting times and less energy waste.
Precise Temperature Control
Induction melting furnaces provide precise temperature control and heat distribution, ensuring a uniform melting process that results in high-quality metal products.
Reduced Material Loss
Induction melting furnaces have a sealed and compact design, which reduces the amount of radiant heat loss. This helps in decreasing metal oxidation and material loss.
Cleaner and Safer Operation
Induction melting furnaces do not require any fuel to create heat, which means there are no harmful emissions produced during the melting process, making it safer and environmentally friendly.
Versatility
Induction melting furnaces can melt various alloys and metals, including steel, aluminum, copper, and brass, making them an ideal choice for many metallurgical applications.
Greater Productivity
Induction melting furnaces can perform multiple melting and pouring operations simultaneously, increasing productivity and reducing downtime.
Cost-Effective
Induction melting furnaces are cost-effective in the long run, especially when compared to traditional melting methods like gas or oil-fired furnaces. They require less maintenance, have a longer lifespan, and operate with greater energy efficiency.
Overall, induction melting furnaces provide a clean, efficient, and precise method for melting metals, which results in high-quality metal products that meet industry standards and customer requirements.